Absolute encoder
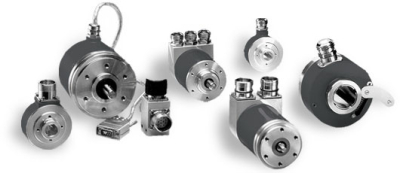
Extensive range of absolute encoders as solid shaft and hollow shaft versions.
The detailed product information for our absolute encoders is currently only available in English. Please click on the following button to view all other contents.
Extensive range of absolute rotary encoders as solid shaft and hollow shaft versions.
Selecting an Absolute encoder Design and function:
Absolute encoders have a disk with a digital coding on concentric tracks. This code is read by a Opto-Asic. A unique bit pattern is assigned to each position. The advantage is, that after power failure true position verification is available as soon as power is up again, even if the shaft was moved during the dead state.
Advantage:
No reference drives after starting-up are necessary as with incremental systems. Safety is increased and the time taken for reference drives is saved.
Selecting an absolute encoder:
When selecting the right absolute encoder the following parameters should be considered in addition to the recomendations on Selecting an Incremental Encoder till Selecting an Absolute Encoder
• Supply voltage
• Type of code
• lnterface(SSl,parallel,fieldbus, 4 ... 20mA)
• Type of code
• lnterface(SSl,parallel,fieldbus, 4 ... 20mA)
Versions:
Singleturn encoders:
Depending on the number of divisions they genrate up to 131072 (17 Bit) unique per turn. This corresponds to an angular resolution of 0,0028°. After one revolution the process re-starts. Singleturn encoders can be used in applications where revolution is sufficient, e.g. measurement of angles, robotic.
Multiturn encoders:
They are available with up to 131072 (17 Bit) definite angular positions per revolution and in addition 4096 (12 Bit) definite revolutions. This corresponds to 70 billion definite positions. Multiturn encoders can be used for positioning applications e.g. automatic storage, retiered systems, litt elevators, cranes, machine tool, etc.