Systems
Bus systems:
The use of a network of sensor-actuator bus systems has essential advantages:
• Reduced expenditure concerning connection: All members are linked by one cable.
• Wide range diagnostics and programming possibility of the units.
In the following please find the available bus systems:
• Reduced expenditure concerning connection: All members are linked by one cable.
• Wide range diagnostics and programming possibility of the units.
In the following please find the available bus systems:
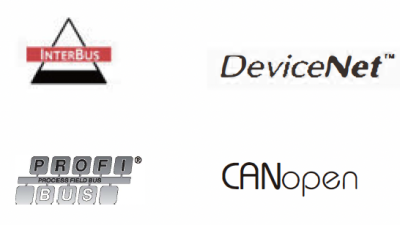
CAN:
- CAN fullfils the real time demands of the automobile industries (ABS, Airbag, Motormanagement)
- Multi-Master system
- The message text (speed, position ... ) itself is marked by an identifier through the whole network, instead of indexing the nodes.
- Check for importance of message
- Accept or ignore ® network wide broadcasting
- high allocation on the network
- Monitoring (high reliability)
- Bus Specification according to CAN High Speed ISO/DIN 11898 for transmission rates of up to 1 Mbaud.
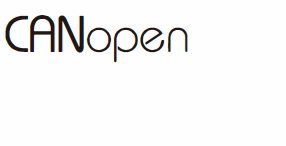
Introduction
The Meyle CANopen encoder is an absolute encoder. The version described sends its current position to another station via the
"CAN-bus" transmission medium (physically: screened and twisted two-wire line).
The serial bus system CAN (Controller Area Network), which had been originally developed for automotive uses, is gaining ground in industrial automation technology. The system is multimaster compatible, i.e. several CAN- stations are able to request the bus at the same time. The data transfer is regulated by the message's priority. The message with the highest priority (determined by the identifier) will be received immediately. Within the CAN system, there are message identifiers but no transport addresses. The message which is being sent can be received by all stations at the same time (broadcast). By means of a special filter method, the station only accepts the relevant
"CAN-bus" transmission medium (physically: screened and twisted two-wire line).
The serial bus system CAN (Controller Area Network), which had been originally developed for automotive uses, is gaining ground in industrial automation technology. The system is multimaster compatible, i.e. several CAN- stations are able to request the bus at the same time. The data transfer is regulated by the message's priority. The message with the highest priority (determined by the identifier) will be received immediately. Within the CAN system, there are message identifiers but no transport addresses. The message which is being sent can be received by all stations at the same time (broadcast). By means of a special filter method, the station only accepts the relevant
messages which is of importance for this station. The identifier transmitted with the message is the basis for the decision as to whether the message will be accepted or not.
The bus coupler is standardised according to the international standard ISO-DIS 11898 (CAN High Speed) and allows data to be transferred at a maximum rate of 1 MBit/s. The most significant feature of the
CAN-protocol is its high level of transmission reliability (Hamming distance = 6). The CANController Intel 82527 used in the encoder is basic as weil as full-CAN compatible and supports the CAN-specification 2.0 part B (standard protocol with 11-bit- identifier as weil as extended protocol with 29-bit identifier).
The bus coupler is standardised according to the international standard ISO-DIS 11898 (CAN High Speed) and allows data to be transferred at a maximum rate of 1 MBit/s. The most significant feature of the
CAN-protocol is its high level of transmission reliability (Hamming distance = 6). The CANController Intel 82527 used in the encoder is basic as weil as full-CAN compatible and supports the CAN-specification 2.0 part B (standard protocol with 11-bit- identifier as weil as extended protocol with 29-bit identifier).
Field of application
In applications, where the position of a drive or of other parts of a machine has to be recorded and signalled to the control system, the encoder can carry out this function. The encoder can resolve, for
instance, positioning tasks by sending the check-back signal concerning the present drive position via the CAN bus to the positioning unit.
The CANopen Profile
CANopen allows for:
• synchronisation of the devices,
• auto-configuration of the network,
• comfortable access to all device parameters.
CANopen uses four communication objects (COB) with different features:
• Process Data Objects (PDO) for real-time data
• Service Data Objects (SDO) for the transfer of parameters and programs
• Network Management (NMT, LifeGuarding)
• predefined objects (for synchronisation, time stamp, emergency message)
• Service Data Objects (SDO) for the transfer of parameters and programs
• Network Management (NMT, LifeGuarding)
• predefined objects (for synchronisation, time stamp, emergency message)
• simultaneous data input and output.
• cyclical and event-controlled process data processing,
• cyclical and event-controlled process data processing,
All device parameters are stored in an object directory. The object directory contains the description, data type and structure of the parameters as weil as their addresses (index).
The directory consists of three parts:
The directory consists of three parts:
• communication
• profile parameters,
• device profile parameters and manufacturer specific parameters.
• profile parameters,
• device profile parameters and manufacturer specific parameters.
The encoder device profile {CIA DSP 406)
This profile describes a standardised and binding, but manufacturer-independent definition of the interface for encoders. The profile not only defines which CANopen functions are to be used, but also how they are to be used. This standard allows an open and manufacturer-independent bus system. The device profile consists of two object categories
- the standard category C1 describes all the basic functions the shaft encoder must contain
- the extended category C2 contains a variety of additional functions which either have to be supported by category C2 shaft encoders (mandatory) or which are optional. Category C2 devices thus contain all C1 and C2 mandatory functions as weil as, depending on the manufacturer, further optional functions. In addition, an addressable area is defined in the profile, to which, depending on the manufacturer, different functions can be assigned.
DATA Transmission
In CANopen, the data is transferred by means of two different communication types (COB = Communication Object) with different features:
• Process Data Objects (PDO)
• Service Data Objects (SDO)
The priority of the message objects is determined by the COB identifier. The process data objects (PDO) serve the highly dynamic exchange of real-time data (e.g. position of the shaft encoder) with a maximum length of 8 Byte.
This data is transferred with high priority {low COB identifier). PDOs are broadcast messages and put their information simultaneously at the disposal of all desired receivers. The service data objects (SDO) form the communication channel for the transfer of device parameters (e.g. programming of the shaft encoder's resolution). Since these parameters are transferred acyclically (e.g. only once when starting up the network), the SDO objects have a low priority {high COB identifier).
Profibus: General Information
The basic functions of the PROFIBUS DP are only described in extracts in here. For additional information, please refer to
the standards on PROFIBUS DP, i.e. DIN 19245-3 and EN 50170 respectively.
lntroduction
The Meyle Profibus encoders are absolute encoders. The version described sends its current position to another station via the transmission medium "PROFIBUS DP" (physically: screened and twisted pair line). The Profibus encoder supports all class 1 and 2 functions listed in the encoder profile . PROFIBUS-DP is standardised and binding, but manufacturer-independent definition for a variety of applications in the field of production, process and automation. The requirements of openness and independence from the manufacturer are stipulated in the European standard EN 50 170.
PROFIBUS-DP permits the communication of devices produced by different manufacturers without any particular adaptations of the interfaces. PROFIBUS DP is a special standard version for a quick data exchange within the field level which has been optimised in terms of speed and low connection costs. Central with local field devices like drives, valves, or encoders. The data exchange between these devices is predominantly cyclical. The communication functions required for this exchange are determined by the functions of the PROFIBUS DP according to the EN 50 170 European standard.
Field of application
In systems, where the position of a drive or of any other part of a machine has to be recorded and transmitted to the control system, the encoder is doing this function. The encoder can resolve, for instance,
positioning tasks by sending the feedback signal concerning the present drive position via the PROFIBUS DP to the positioning unit.
Basic function of the Profibus DP
The central control system (master) cyclically reads out the input information from the slaves and transmits the output information to the slaves. For this purpose, the bus cycle time has to be shorter than the program cycle time of the central control system
(e.g. SPC, or IPC), which amounts to approx. 10 ms for several applications. Beside the
(e.g. SPC, or IPC), which amounts to approx. 10 ms for several applications. Beside the
cyclical user data transfer, the PROFIBUS DP version also disposes of powerful functions for diagnosis and initial operation procedures. The data traffic is controlled by watchdog functions on both the slave and the master side. In the following the basic functions of the PROFI BUS DP are summarised in short.
Transmission technology:
• Stop: only master-master data transfer is possible
• Clear: The input data are read, the output data remain in the safe status
• Clear: The input data are read, the output data remain in the safe status
• RS-485 twisted pair line
• Baud rates ranging from 9.6 kbit/s up to 12 Mbit/s
• Baud rates ranging from 9.6 kbit/s up to 12 Mbit/s
• Maximum of 246 byte input and output data per DP slave possible
• Synchronisation of in- and/ or output
• Synchronisation of in- and/ or output
Bus access:
- Monomaster or multimaster systems possible
- Token passing procedure between the masters and master-slave procedures for slaves
- Master and slave devices, max. of 126 stations at a single bus
Synchronisation:
- Control commands enable a synchronisation of the input and output data
- Sync mode: Output data are being synchronised
Protection functions:
• Access protection of the DP slaves' input/output
• All messages are transferred with a hamming distance of HD=4
• Response control at the DP slaves
• Monitoring of the user data communication with adjustable control timer at the master
Communication:
• Point-to-point (user data communication) or multicas (control commands)
• Cyclical master-slave user data communication and acyclical master-master data transfer
• Cyclical master-slave user data communication and acyclical master-master data transfer
Functionality:
• Address assignment for the DP slaves via the bus
• Cyclical user data transfer between DP master and DP slave(s)
• Configuration of the DP master (DPM1) via the bus
• Single DP slaves are dynamically activated or deactivated
• Control of the DP slave's configuration.
• Powerful diagnostic functions, 3 stepped diagnostic message levels.
• Cyclical user data transfer between DP master and DP slave(s)
• Configuration of the DP master (DPM1) via the bus
• Single DP slaves are dynamically activated or deactivated
• Control of the DP slave's configuration.
• Powerful diagnostic functions, 3 stepped diagnostic message levels.
Device types:
• DP master class 2 (DPM2), e.g. programming/ project planning devices
• DP master class 1 (DPM1), e.g. central automation devices like SPC, PC
• DP slave e. g. devices with binary or analogue input/output, drives, valves
• DP master class 1 (DPM1), e.g. central automation devices like SPC, PC
• DP slave e. g. devices with binary or analogue input/output, drives, valves
Operating state:
Operate: cyclical transfer of input and output data
Diagnostic function
The extensive diagnostic functions of PROFIBUS DP allow a quick localisation of possible errors. The diagnostic messages
are transmitted by means of the bus and are joined together at the master.
System Performance
To ensure a high level of exchangeability between the devices, the system performance of PROFIBUS DP has also been standardised. lt is mainly determined by the operational status of the DPM1. The DPM1 can either be controlled locally or via the bus by the project planning device. The following three main states are available:
Operate
The DPM1 has entered the data transfer phase. In case of a cyclical data traffic, the input is read by the DP slaves while the output is transferred to the DP slaves. After an error has occurred during the data transfer phase of the DPM1, like for example, the failure of a DP slave, the response of the system is determined by the operating parameter "Auto Clear". lf this parameter has
been set to true, the DPM1 will set the output of all the respective DP slaves to the safe status, as soon as a DP slave is no longer available for user data communication. Afterwards, the DPM1 changes to the clear status. lt this parameter is = false, the DPM1 remains, even if an error occurs, in the operate status, and the user can determine the response of the system at his own decision.
Stop
There is no data traffic between DPM1 and the DP slaves.
Clear
The DPM1 reads the input information of the DP slaves and maintains the safe status of the DP slaves' output.
Cyclical data transfer between DPM1 and the DP SLAVES
The data traffic between the DPM1 and the respective DP slaves is automatically handled by the DPM1 in a fixed, recurring order. When configuring the bus system, the user assigns a DP slave to the DPM1. In addition the slaves are in- or excluded from the user data communication. The data traffic between the DPM1 and the DP slaves is subdivided in three phases: parameterisation, configuration, and data transfer. Before including a DP slave in the data transfer phase, the DPM1 checks during the parameterisation and configuration phase,
whether the planned set configuration corresponds to the actual configuration of the device. For this check, the device type, the information on the format and the length as weil as the number of input and output lines have to be correct. Due to this check it is ensured that the parameterisation is reliable and correct at the end. In addition to the user communication, which is automatically executed by the DPM1, the user can request the new parameterisation data to be sent to the DP slaves.
Profile
PROFINET, launched by PROFIBUS International (PI), is a new-generation industrial-ethernet-technology-based automation bus standard. PROFINET provides a sound and complete network solution for automation communi-
cation, including topical issues in the field of automation such as real-time Ethernet, motion control, distributed automation, fail-safe and network security. This crosssupplier technology is compatible with industrial Ethernet and existing profibus technology to protect existing investment.
Technology
To achieve the above communication functions, the following three communication protocol levels are defined. [1]
• TCP/IP is for PROFINET CBA and factory debugging, with a response time of about 100ms.
• RT (real-time) communication protocol is for PROFINET CBA and PROFINET 10, with a response time of less than 1 Oms.
• TCP/IP is for PROFINET CBA and factory debugging, with a response time of about 100ms.
• RT (real-time) communication protocol is for PROFINET CBA and PROFINET 10, with a response time of less than 1 Oms.
IRT 0sochronous real-time) communication protocol is for PROFINET 10 communication of the drive system, with a response time of less than 1 ms. Ethernet analysis tools help to record and display the packets of the PROFINET communication protocol. Some software interpret PROFINET data frames.
PROFINET component model
A PROFINET CBA system includes many automated components, mechanical, electronic or IT variables generated by standard programming tools. Components are described by PROFINET Component Description (PCD) files in XML format. Planning tools load these descriptions and establish logical relationships between the different components. This mode is considerably influenced by the EC 61499 standard. The basic concept of PROFINET CBA is that many times the automation system can be divided into several small subsystems, clear1y
distinguished from each other. PROFINET components are generally controlled by only a few input signals. With these components, the program written by the user activates a specific function in the component and transmits the output signal to another, using a maker-neutral technology. Component-based communication requires only planning, not programming. PROFINET CBA communication (non-real-time communication) is suitable for systems with a bus cycle time of 50-100 ms.
PROFINET and peripherals
PROFINET network communicates with external devices through PROFINET 10. PROFINET 10 defines the communication function of external devices connected to the field. lts basis is the real-time concept of cascading. PROFINET 10 defines the controller (with "master function" equipment) and other equipment (with "slave function" equipment) complete data exchange, parameter setting and diagnosis functions. PROFINET 10 is designed to provide fast data transmission between Ethernet-connected devices and supports the provider-consumer model. Devices that support the PROFI BUS communication protocol can be seamlessly connected to the PROFINET network without the need for IO-proxy and other devices. Device developers may use commercially available Ethernet controllers to develop PROFINET 10 devices. PROFINET 10 is suitable for systems with network cycle times of several milliseconds. [2]
PROFINET 10 system package:
• 10 controller that controls the automated task.
• 10 devices, generally field devices controlled and monitored by 10 controller. One 10 device may include several modules or sub-modules.
• 10 monitor, a PC software, can set param eters and diagnose the status of individual modules.
PROFINET 10 establishes an application relation (AR) between the 10 controller and the 10 device, in which communication relations (CR) with different characteristics such as parameter transmission, periodic data exchange, and warning processing are defined.
• 10 controller that controls the automated task.
• 10 devices, generally field devices controlled and monitored by 10 controller. One 10 device may include several modules or sub-modules.
• 10 monitor, a PC software, can set param eters and diagnose the status of individual modules.
PROFINET 10 establishes an application relation (AR) between the 10 controller and the 10 device, in which communication relations (CR) with different characteristics such as parameter transmission, periodic data exchange, and warning processing are defined.
PROFINET 10 Addressing
Each module in the PROFINET network has the following three addresses:
• MAC addresso
• IP addresso
• Device name is the logical name defined for the module in the entire network configuration. Since PROFINET uses TCP/P, MAC address and IP address are used. In case a device is replaced with another, its MAC address changes, and the IP address is the result
• MAC addresso
• IP addresso
• Device name is the logical name defined for the module in the entire network configuration. Since PROFINET uses TCP/P, MAC address and IP address are used. In case a device is replaced with another, its MAC address changes, and the IP address is the result
of dynamic addressing. To have a fixed name for a certain device on the network, a device is named.
To assign IP addresses, subnet masks and default gateways, the following two methods are defined:
DCP (Protocol) (Discovery and Configuration Protocol).
DHCP (Dynamic Hast Configuration Protocol).
To assign IP addresses, subnet masks and default gateways, the following two methods are defined:
DCP (Protocol) (Discovery and Configuration Protocol).
DHCP (Dynamic Hast Configuration Protocol).
PROFINET and real-time
In the PROFINET 10 network, program data and warnings are transmitted in real time. The real-time of PROF-INET is according to the definition of IEEE and IEC, which allows real-time services to be processed within a limited time within a network cycle. Real-time communication is the basis for PROFINET 10 data
exchange. When processing, the real-time data is higher than that of TCP (UDPVIP data in priority. PROFINET RT, the basis for decentralized peripheral real-time communication, is also for the PROFINET component model (PROFINET CBA). The bus cycle time for general data exchange is within hundreds of microseconds.
PROFINET and lsochronous Communication
The isochronous data exchange of PROFINET is defined in the isochronous real time (IRT) function. PROFINET 10 field devices with IRT functionality have switch ports integrated in the field devices and can be based on Ethernet controllers ERTEC 400/200.The bus cycle time for general data exchange is from hundreds of milliseconds to several micro-
seconds. The difference between isochronous communication and real-time communication is that the former features a high degree of certainty. The start time of the bus cycle can be maintained to a high accuracy with a jitter of up to 1 µs. Motion control applications like motor position control programs use isochronous real-time communication.
Application profile
Application profile (profile) is a special device or a pre-defined function and feature configuration for a special application. The PROFINET application profile is formulated by the PI (PROFIBUS & PROFINET International Association) working group and issued by PI. Application profiles contribute to the openness, interoperability and interchangeability of equipment, so end users can be sure that similar equipment provided by different equipment manufacturers will have standardized functions and usage methods.
Choices by users promote the competition of equipment manufacturers, which improves the function of the product and lowers the cost. PROFINET has many application profiles, such as for encoders, PROFldriveand PROFIsafe. There are even dedicated application profiles for trains. In 2009, German automakers proposed the PROFlenergy application profile, which mainly manages energy consumption during vehicle manufacturing.