Sistemas
Sistemas de computadores buses:
La utilización de una red de sistemas bus sensor-actuador presenta ventajas esenciales:
- Reducción de los gastos relativos a la conexión: Todos los miembros están conectados por un solo cable.
- Amplia posibilidad de diagnóstico y programación de las unidades.
A continuación encontrará los sistemas de bus disponibles:
- Reducción de los gastos relativos a la conexión: Todos los miembros están conectados por un solo cable.
- Amplia posibilidad de diagnóstico y programación de las unidades.
A continuación encontrará los sistemas de bus disponibles:
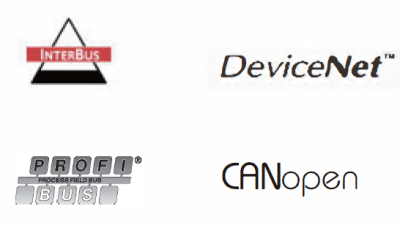
CAN:
- CAN satisface las demandas en tiempo real de la industria del automóvil (ABS, airbag, gestión del motor)
- Sistema multimaestro
- El propio texto del mensaje (velocidad, posición ... ) está marcado por un identificador a través de toda la red, en lugar de indexar los nodos.
- Comprobar la importancia del mensaje
- Aceptar o ignorar ® difusión en toda la red
- alta asignación en la red
- Supervisión (alta fiabilidad)
- Especificación de bus según CAN High Speed ISO/DIN 11898 para velocidades de transmisión de hasta 1 Mbaud.
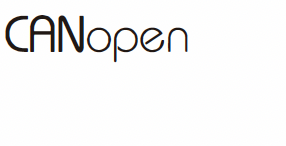
Introducción
El encóder CANopen de Meyle es un encóder absoluto. La versión descrita envía su posición actual a otra estación a través del medio de transmisión "CAN-bus"
(físicamente: línea de dos hilos apantallada y trenzada).
El sistema de bus serie CAN (Controller Area Network), que se había desarrollado originalmente para usos automovilísticos, está ganando terreno en la tecnología de automatización industrial. El sistema es compatible con multimaestro, es decir, varias estaciones CAN pueden solicitar el bus al mismo tiempo. La transferencia de datos está regulada por la prioridad del mensaje. El mensaje con la prioridad más alta (determinada por el identificador) se recibirá inmediatamente. En el sistema CAN existen identificadores de mensajes, pero no direcciones de transporte. El mensaje que se envía puede ser recibido por todas las estaciones al mismo tiempo (broadcast). Mediante un método de filtrado especial, la estación sólo acepta los
(físicamente: línea de dos hilos apantallada y trenzada).
El sistema de bus serie CAN (Controller Area Network), que se había desarrollado originalmente para usos automovilísticos, está ganando terreno en la tecnología de automatización industrial. El sistema es compatible con multimaestro, es decir, varias estaciones CAN pueden solicitar el bus al mismo tiempo. La transferencia de datos está regulada por la prioridad del mensaje. El mensaje con la prioridad más alta (determinada por el identificador) se recibirá inmediatamente. En el sistema CAN existen identificadores de mensajes, pero no direcciones de transporte. El mensaje que se envía puede ser recibido por todas las estaciones al mismo tiempo (broadcast). Mediante un método de filtrado especial, la estación sólo acepta los
mensajes que es de importancia para esta estación. El identificador transmitido con el mensaje es la base para decidir si el mensaje será aceptado o no.
El acoplador de bus está normalizado según la norma internacional ISO-DIS 11898 (CAN High Speed) y permite transferir datos a una velocidad máxima de 1 MBit/s. La característica más significativa del protocolo CAN
es su alto nivel de fiabilidad de transmisión (distancia Hamming = 6). El controlador CAN Intel 82527 utilizado en el codificador es compatible tanto con CAN básico como con CAN completo y admite la especificación CAN 2.0 parte B (protocolo estándar con identificador de 11 bits y protocolo ampliado con identificador de 29 bits).
El acoplador de bus está normalizado según la norma internacional ISO-DIS 11898 (CAN High Speed) y permite transferir datos a una velocidad máxima de 1 MBit/s. La característica más significativa del protocolo CAN
es su alto nivel de fiabilidad de transmisión (distancia Hamming = 6). El controlador CAN Intel 82527 utilizado en el codificador es compatible tanto con CAN básico como con CAN completo y admite la especificación CAN 2.0 parte B (protocolo estándar con identificador de 11 bits y protocolo ampliado con identificador de 29 bits).
Ámbito de aplicación
En aplicaciones en las que la posición de un accionamiento o de otras partes de una máquina debe registrarse y señalarse al sistema de control, el encóder puede desempeñar esta función. El encóder puede resolver, por ejemplo, tareas de posicionamiento enviando la señal de comprobación relativa a la posición actual del accionamiento a través del bus CAN a la unidad de posicionamiento.
El perfil CANopen
CANopen permite:
- sincronización de los dispositivos,
- autoconfiguración de la red,
- acceso cómodo a todos los parámetros de los dispositivos.
CANopen utiliza cuatro objetos de comunicación (COB) con diferentes características:
- Objetos de datos de proceso (PDO) para datos en tiempo real
- Objetos de datos de servicio (SDO) para la transferencia de parámetros y programas
- Gestión de red (NMT, LifeGuarding)
- objetos predefinidos (para sincronización, sello de tiempo, mensaje de emergencia)
- entrada y salida simultánea de datos
- Procesamiento de datos de proceso cíclico y controlado por eventos
Todos los parámetros del aparato se almacenan en un directorio de objetos. El directorio de objetos contiene la descripción, el tipo de datos y la estructura de los parámetros, así como sus direcciones (índice).
El directorio consta de tres partes:
El directorio consta de tres partes:
- comunicación
- parámetros del perfil,
- parámetros del perfil del dispositivo y parámetros específicos del fabricante.
- parámetros del perfil,
- parámetros del perfil del dispositivo y parámetros específicos del fabricante.
El perfil del dispositivo codificador {CIA DSP 406)
Este perfil describe una definición estandarizada y vinculante, pero independiente del fabricante, de la interfaz para codificadores. El perfil no sólo define qué funciones CANopen deben utilizarse, sino también cómo deben utilizarse. Este estándar permite un sistema de bus abierto e independiente del fabricante. El perfil de dispositivo consta de dos categorías de objetos
- la categoría estándar C1 describe todas las funciones básicas que debe contener el codificador rotatorio
- la categoría ampliada C2 contiene una serie de funciones adicionales que deben ser compatibles con los codificadores rotatorios de la categoría C2 (obligatorias) o que son opcionales. Los dispositivos de la categoría C2 contienen, por tanto, todas las funciones obligatorias de C1 y C2, así como, dependiendo del fabricante, otras funciones opcionales. Además, en el perfil se define un área direccionable a la que, dependiendo del fabricante, se pueden asignar diferentes funciones.
DATA Transmission
En CANopen, los datos se transfieren mediante dos tipos de comunicación diferentes (COB = Objeto de Comunicación) con características distintas:
- Objetos de datos de proceso (PDO)
- Objetos de datos de servicio (SDO)
La prioridad de los objetos de mensaje viene determinada por el identificador COB. Los objetos de datos de proceso (PDO) sirven para el intercambio altamente dinámico de datos en tiempo real (por ejemplo, la posición del codificador del eje) con una longitud máxima de 8 Bytes.
Estos datos se transfieren con alta prioridad {identificador COB bajo). Los PDO son mensajes de difusión y ponen su información simultáneamente a disposición de todos los receptores deseados. Los objetos de datos de servicio (SDO) constituyen el canal de comunicación para la transferencia de parámetros del dispositivo (por ejemplo, la programación de la resolución del codificador del eje). Dado que estos parámetros se transfieren de forma acíclica (por ejemplo, sólo una vez al iniciar la red), los objetos SDO tienen una prioridad baja {identificador COB alto).
Profibus: Información general
The basic functions of the PROFIBUS DP are only described in extracts in here. For additional information, please refer to
the standards on PROFIBUS DP, i.e. DIN 19245-3 and EN 50170 respectively.
lntroduction
The Meyle Profibus encoders are absolute encoders. The version described sends its current position to another station via the transmission medium "PROFIBUS DP" (physically: screened and twisted pair line). The Profibus encoder supports all class 1 and 2 functions listed in the encoder profile . PROFIBUS-DP is standardised and binding, but manufacturer-independent definition for a variety of applications in the field of production, process and automation. The requirements of openness and independence from the manufacturer are stipulated in the European standard EN 50 170.
PROFIBUS-DP permits the communication of devices produced by different manufacturers without any particular adaptations of the interfaces. PROFIBUS DP is a special standard version for a quick data exchange within the field level which has been optimised in terms of speed and low connection costs. Central with local field devices like drives, valves, or encoders. The data exchange between these devices is predominantly cyclical. The communication functions required for this exchange are determined by the functions of the PROFIBUS DP according to the EN 50 170 European standard.
Field of application
In systems, where the position of a drive or of any other part of a machine has to be recorded and transmitted to the control system, the encoder is doing this function. The encoder can resolve, for instance,
positioning tasks by sending the feedback signal concerning the present drive position via the PROFIBUS DP to the positioning unit.
Basic function of the Profibus DP
The central control system (master) cyclically reads out the input information from the slaves and transmits the output information to the slaves. For this purpose, the bus cycle time has to be shorter than the program cycle time of the central control system
(e.g. SPC, or IPC), which amounts to approx. 10 ms for several applications. Beside the
(e.g. SPC, or IPC), which amounts to approx. 10 ms for several applications. Beside the
cyclical user data transfer, the PROFIBUS DP version also disposes of powerful functions for diagnosis and initial operation procedures. The data traffic is controlled by watchdog functions on both the slave and the master side. In the following the basic functions of the PROFI BUS DP are summarised in short.
Transmission technology:
• Stop: only master-master data transfer is possible
• Clear: The input data are read, the output data remain in the safe status
• Clear: The input data are read, the output data remain in the safe status
• RS-485 twisted pair line
• Baud rates ranging from 9.6 kbit/s up to 12 Mbit/s
• Baud rates ranging from 9.6 kbit/s up to 12 Mbit/s
• Maximum of 246 byte input and output data per DP slave possible
• Synchronisation of in- and/ or output
• Synchronisation of in- and/ or output
Bus access:
- Monomaster or multimaster systems possible
- Token passing procedure between the masters and master-slave procedures for slaves
- Master and slave devices, max. of 126 stations at a single bus
Synchronisation:
- Control commands enable a synchronisation of the input and output data
- Sync mode: Output data are being synchronised
Protection functions:
• Access protection of the DP slaves' input/output
• All messages are transferred with a hamming distance of HD=4
• Response control at the DP slaves
• Monitoring of the user data communication with adjustable control timer at the master
Communication:
• Point-to-point (user data communication) or multicas (control commands)
• Cyclical master-slave user data communication and acyclical master-master data transfer
• Cyclical master-slave user data communication and acyclical master-master data transfer
Functionality:
• Address assignment for the DP slaves via the bus
• Cyclical user data transfer between DP master and DP slave(s)
• Configuration of the DP master (DPM1) via the bus
• Single DP slaves are dynamically activated or deactivated
• Control of the DP slave's configuration.
• Powerful diagnostic functions, 3 stepped diagnostic message levels.
• Cyclical user data transfer between DP master and DP slave(s)
• Configuration of the DP master (DPM1) via the bus
• Single DP slaves are dynamically activated or deactivated
• Control of the DP slave's configuration.
• Powerful diagnostic functions, 3 stepped diagnostic message levels.
Device types:
• DP master class 2 (DPM2), e.g. programming/ project planning devices
• DP master class 1 (DPM1), e.g. central automation devices like SPC, PC
• DP slave e. g. devices with binary or analogue input/output, drives, valves
• DP master class 1 (DPM1), e.g. central automation devices like SPC, PC
• DP slave e. g. devices with binary or analogue input/output, drives, valves
Operating state:
Operate: cyclical transfer of input and output data
Diagnostic function
The extensive diagnostic functions of PROFIBUS DP allow a quick localisation of possible errors. The diagnostic messages
are transmitted by means of the bus and are joined together at the master.
System Performance
To ensure a high level of exchangeability between the devices, the system performance of PROFIBUS DP has also been standardised. lt is mainly determined by the operational status of the DPM1. The DPM1 can either be controlled locally or via the bus by the project planning device. The following three main states are available:
Operate
The DPM1 has entered the data transfer phase. In case of a cyclical data traffic, the input is read by the DP slaves while the output is transferred to the DP slaves. After an error has occurred during the data transfer phase of the DPM1, like for example, the failure of a DP slave, the response of the system is determined by the operating parameter "Auto Clear". lf this parameter has
been set to true, the DPM1 will set the output of all the respective DP slaves to the safe status, as soon as a DP slave is no longer available for user data communication. Afterwards, the DPM1 changes to the clear status. lt this parameter is = false, the DPM1 remains, even if an error occurs, in the operate status, and the user can determine the response of the system at his own decision.
Stop
There is no data traffic between DPM1 and the DP slaves.
Clear
The DPM1 reads the input information of the DP slaves and maintains the safe status of the DP slaves' output.
Cyclical data transfer between DPM1 and the DP SLAVES
The data traffic between the DPM1 and the respective DP slaves is automatically handled by the DPM1 in a fixed, recurring order. When configuring the bus system, the user assigns a DP slave to the DPM1. In addition the slaves are in- or excluded from the user data communication. The data traffic between the DPM1 and the DP slaves is subdivided in three phases: parameterisation, configuration, and data transfer. Before including a DP slave in the data transfer phase, the DPM1 checks during the parameterisation and configuration phase,
whether the planned set configuration corresponds to the actual configuration of the device. For this check, the device type, the information on the format and the length as weil as the number of input and output lines have to be correct. Due to this check it is ensured that the parameterisation is reliable and correct at the end. In addition to the user communication, which is automatically executed by the DPM1, the user can request the new parameterisation data to be sent to the DP slaves.
Profile
PROFINET, launched by PROFIBUS International (PI), is a new-generation industrial-ethernet-technology-based automation bus standard. PROFINET provides a sound and complete network solution for automation communi-
cation, including topical issues in the field of automation such as real-time Ethernet, motion control, distributed automation, fail-safe and network security. This crosssupplier technology is compatible with industrial Ethernet and existing profibus technology to protect existing investment.
Technology
To achieve the above communication functions, the following three communication protocol levels are defined. [1]
• TCP/IP is for PROFINET CBA and factory debugging, with a response time of about 100ms.
• RT (real-time) communication protocol is for PROFINET CBA and PROFINET 10, with a response time of less than 1 Oms.
• TCP/IP is for PROFINET CBA and factory debugging, with a response time of about 100ms.
• RT (real-time) communication protocol is for PROFINET CBA and PROFINET 10, with a response time of less than 1 Oms.
IRT 0sochronous real-time) communication protocol is for PROFINET 10 communication of the drive system, with a response time of less than 1 ms. Ethernet analysis tools help to record and display the packets of the PROFINET communication protocol. Some software interpret PROFINET data frames.
PROFINET component model
A PROFINET CBA system includes many automated components, mechanical, electronic or IT variables generated by standard programming tools. Components are described by PROFINET Component Description (PCD) files in XML format. Planning tools load these descriptions and establish logical relationships between the different components. This mode is considerably influenced by the EC 61499 standard. The basic concept of PROFINET CBA is that many times the automation system can be divided into several small subsystems, clear1y
distinguished from each other. PROFINET components are generally controlled by only a few input signals. With these components, the program written by the user activates a specific function in the component and transmits the output signal to another, using a maker-neutral technology. Component-based communication requires only planning, not programming. PROFINET CBA communication (non-real-time communication) is suitable for systems with a bus cycle time of 50-100 ms.
PROFINET and peripherals
PROFINET network communicates with external devices through PROFINET 10. PROFINET 10 defines the communication function of external devices connected to the field. lts basis is the real-time concept of cascading. PROFINET 10 defines the controller (with "master function" equipment) and other equipment (with "slave function" equipment) complete data exchange, parameter setting and diagnosis functions. PROFINET 10 is designed to provide fast data transmission between Ethernet-connected devices and supports the provider-consumer model. Devices that support the PROFI BUS communication protocol can be seamlessly connected to the PROFINET network without the need for IO-proxy and other devices. Device developers may use commercially available Ethernet controllers to develop PROFINET 10 devices. PROFINET 10 is suitable for systems with network cycle times of several milliseconds. [2]
PROFINET 10 system package:
• 10 controller that controls the automated task.
• 10 devices, generally field devices controlled and monitored by 10 controller. One 10 device may include several modules or sub-modules.
• 10 monitor, a PC software, can set param eters and diagnose the status of individual modules.
PROFINET 10 establishes an application relation (AR) between the 10 controller and the 10 device, in which communication relations (CR) with different characteristics such as parameter transmission, periodic data exchange, and warning processing are defined.
• 10 controller that controls the automated task.
• 10 devices, generally field devices controlled and monitored by 10 controller. One 10 device may include several modules or sub-modules.
• 10 monitor, a PC software, can set param eters and diagnose the status of individual modules.
PROFINET 10 establishes an application relation (AR) between the 10 controller and the 10 device, in which communication relations (CR) with different characteristics such as parameter transmission, periodic data exchange, and warning processing are defined.
PROFINET 10 Addressing
Each module in the PROFINET network has the following three addresses:
• MAC addresso
• IP addresso
• Device name is the logical name defined for the module in the entire network configuration. Since PROFINET uses TCP/P, MAC address and IP address are used. In case a device is replaced with another, its MAC address changes, and the IP address is the result
• MAC addresso
• IP addresso
• Device name is the logical name defined for the module in the entire network configuration. Since PROFINET uses TCP/P, MAC address and IP address are used. In case a device is replaced with another, its MAC address changes, and the IP address is the result
of dynamic addressing. To have a fixed name for a certain device on the network, a device is named.
To assign IP addresses, subnet masks and default gateways, the following two methods are defined:
DCP (Protocol) (Discovery and Configuration Protocol).
DHCP (Dynamic Hast Configuration Protocol).
To assign IP addresses, subnet masks and default gateways, the following two methods are defined:
DCP (Protocol) (Discovery and Configuration Protocol).
DHCP (Dynamic Hast Configuration Protocol).
PROFINET and real-time
In the PROFINET 10 network, program data and warnings are transmitted in real time. The real-time of PROF-INET is according to the definition of IEEE and IEC, which allows real-time services to be processed within a limited time within a network cycle. Real-time communication is the basis for PROFINET 10 data
exchange. When processing, the real-time data is higher than that of TCP (UDPVIP data in priority. PROFINET RT, the basis for decentralized peripheral real-time communication, is also for the PROFINET component model (PROFINET CBA). The bus cycle time for general data exchange is within hundreds of microseconds.
PROFINET and lsochronous Communication
The isochronous data exchange of PROFINET is defined in the isochronous real time (IRT) function. PROFINET 10 field devices with IRT functionality have switch ports integrated in the field devices and can be based on Ethernet controllers ERTEC 400/200.The bus cycle time for general data exchange is from hundreds of milliseconds to several micro-
seconds. The difference between isochronous communication and real-time communication is that the former features a high degree of certainty. The start time of the bus cycle can be maintained to a high accuracy with a jitter of up to 1 µs. Motion control applications like motor position control programs use isochronous real-time communication.
Application profile
Application profile (profile) is a special device or a pre-defined function and feature configuration for a special application. The PROFINET application profile is formulated by the PI (PROFIBUS & PROFINET International Association) working group and issued by PI. Application profiles contribute to the openness, interoperability and interchangeability of equipment, so end users can be sure that similar equipment provided by different equipment manufacturers will have standardized functions and usage methods.
Choices by users promote the competition of equipment manufacturers, which improves the function of the product and lowers the cost. PROFINET has many application profiles, such as for encoders, PROFldriveand PROFIsafe. There are even dedicated application profiles for trains. In 2009, German automakers proposed the PROFlenergy application profile, which mainly manages energy consumption during vehicle manufacturing.