The effects of arcs
The occurrence of arcs is prevented to the greatest possible extent by
- the use of reliable switch units
- the appropriate fitting of these switch units
- careful quality assurance measures for factory- assembled type-tested switch units.
Nevertheless, arcing cannot be absolutely reliably precluded. Hazard factors result from external effects, improper or unsatisfactory maintenance and finally human error.
In order to restrict the effects of arcing and, above all, to protect the operators from injury, the switch units must be appropriately mechanically designed.
However, the safety measures must not be Iimited to the switch units. The pressure generated by an arc is reduced through pressure relief openings in the switchgear room and increases the pressure there.
The arc detection system LBW is equipped with lightsensitive sensors which immediately detect the occurrence of internal arcs.
This means that the effective duration of the arc is considerably shortened and the gas discharge from the switch unit is appropriately reduced.
The consequence; lower thermal load on the switch units. The rise of pressure in the switchgear building is reduced. The equipment and switchgear room become less sooted. The discharge of poisonous gases is reduced. Reduction of the damage inside the switchgear through the avoidance of the thermo phase.
German standard DIN VDE 0670, part 6, calls for the maximum possible staff safety. In other word, arcing must be prevented altogether or the duration of arcing must be Iimited.
For this purpose Iightsensitive detectors may be employed according to DIN VDE 0670, part 6, table AAZ. Thus, safety against arcing may be achieved in many cases without any additional measures according to DIN VDE 0670, part 601 .
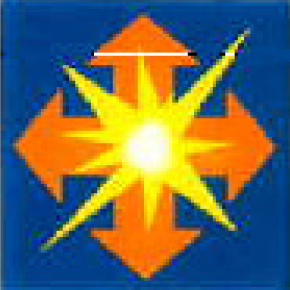
Hazard for switchgear stability due to rise of pressure.
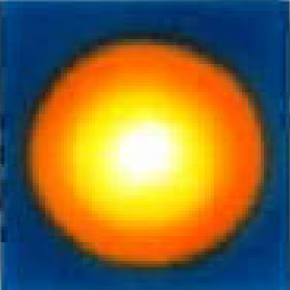
Thermal load on switch units through heat emission of the arc.
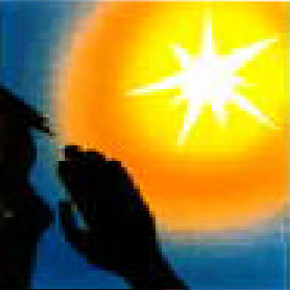
Staff endangered by direct arc radiation and following damage of protective external enclosure.
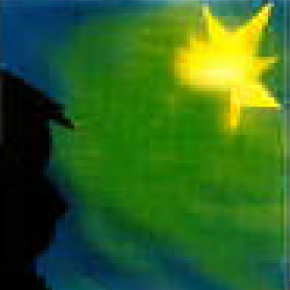
Staff endangered by discharge of hot poisonous gases, decomposition prod- ucts and conductive metal vapours.
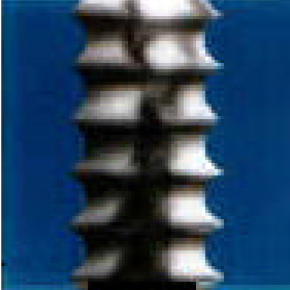
Deposition of conductive combustion products (soot) in the switch unit. The consequence is a reduction of the switchgear insulation level.
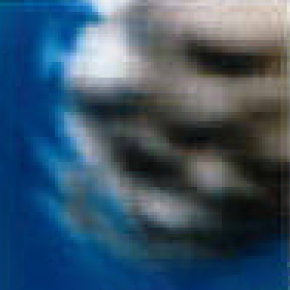
Switch unit and switchgear room filled with smoke. Visibility is impaired.
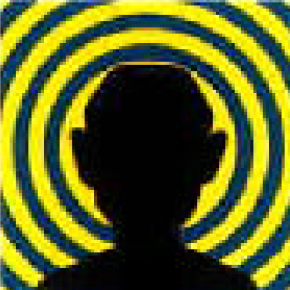
Sound level above the threshold of pain.
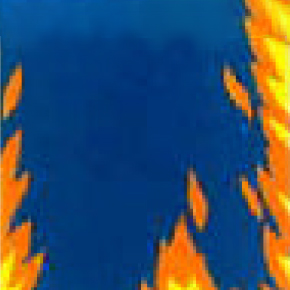
Secondary damages by continued burning of insulating materials affecting staff, brickwork and concrete reinforcements.
Phases in arcing in an enclosed switchgear
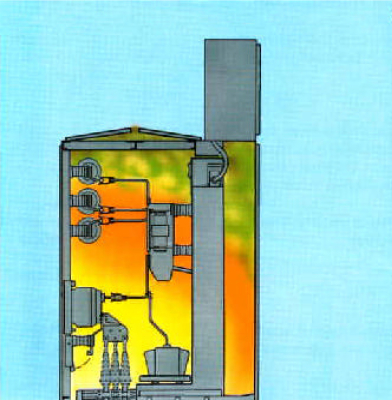
1. Compression phase with maximum excess pressure
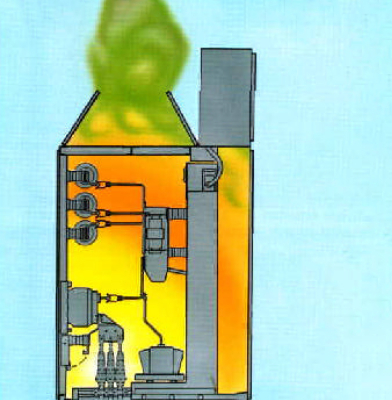
2. Expansion phase with declining pressure
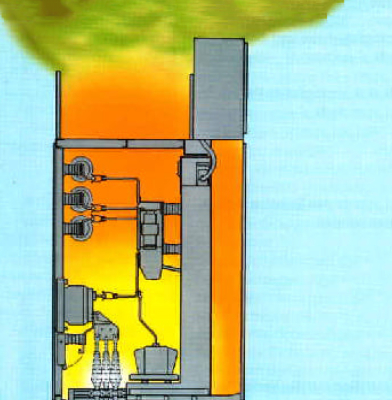
3. Emission phase with discharge of hot air
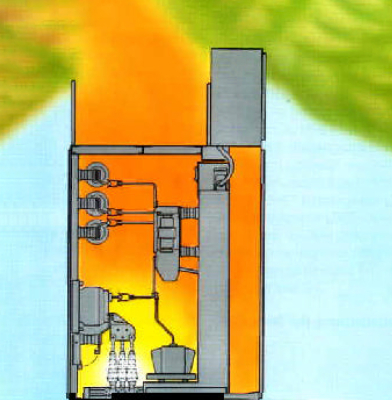
4. Thermo phase with the discharge of metal and vapour from insulating material
The system LBW complies with these requirements
Detection of the arc in its development phase and fast disconnection
Detection by means of lightsensitive detectors and fast disconnection by circuitbreakers.
Maximum possible staff protection
Fast disconnection after 0.1 sec. reduces the load on the switchgear and decreases the gas discharge.
Protection of switchgear
The lower discharge of gas lessens the load of pressure on the building and reduces the thermal effects. Moreover, the surface of the pressure relief openings normally required is substantially reduced.
Improvement of availability
Shorter repair limes following arcing due to reduced load on the switchgear and slighter consequence of damages. As a rule the switchgear room may be entered immediately after the defect. In addition the disturbed areas such as busbar sections, may be detected. The disturbed area is disconnected and the unaffected area remains in service.
Decreasing fire hazard
Fast disconnection interrupts the inlet of heat energy and thus prevents the formation of origins of fire.
Hardening of earlier (open) switchgear
Easy retrofitting of earlier, i. e. open and non-enclosed switchgear is possible. The use of the arc detection System is worth while particularly in installations where the staff safety could not be assured or only with considerable investments.
Arc detection system does not respond to interfering light sources such as portable lamps.
Thanks to its dynamic mode of operation the arc detection system registers only large variations in the density of light.
Am detection System does not respond to interfering electromagnetic influences
Trials and laboratory tests on arcing showed ratings up to 50 kA (peak currents up to 125 kA).
Employment of modern technology
The use of highquality electronic components ensures a high degree of efficiency and reliability.
Inherent safety of SF6-insulated switchgear
The discharge can be prevented of combustion products from SF6-insulated switchgear after arcing.
High economic efficiency
Through the high availability of the switchgear. Minimum requirements on the building and reduction of the extent of damage in the event of arcing.
Improved staff protection during work on switchgear with open enclosure
Method of operation
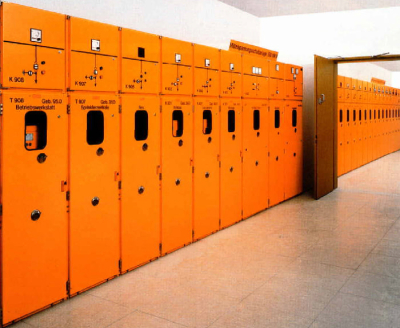
By means of a sensor the radiation emitted by the arc is converted into current. The bandpass filter limits the frequency range to the typical frequencies of arc spectrum and eliminates electro-magnetic interference.
Once the signal from the arc is high enough, it is stored in flip-flop, a display lights up and the relay occurs in a feed-in unit at the same time, the circuit breaker is disconnected. It is also locked against further connections.
By means of an erase key (detect acknowledgement switch) the event may be acknowledged and the interlock of the circuit-breaker be overridden. The feed-in switch may then be actuated again. If the arc detector responds
without the occurrence of overcurrent, a display lights up, too. Through an acknowledgement switch this display may be erased. The equipment parts like transformers, overcurrent relays and circuit-breakers needed for disconnection of the affected area, are part of the switchgear in any case.
Special merits ot the arc detection System LBW
At all times the number of sensors may be increased externally to 20 maximum. In the system LBW the poles cannot be confused and the system remains fully serviceable for approx. 2.0 sec. following failure of the supply voltage.
The system LBW detects even the weakest arcs.
The System LBW is insensitive to mechanical release such as by touching and vibration.
Even if the sensors are destroyed by the arc, the occurrence of an arc is detected because the storage of the control signal in the amplifier takes less than 1 msec.
Protected areas
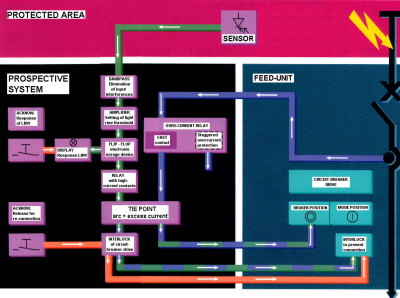
Planning the arc detection system LBW
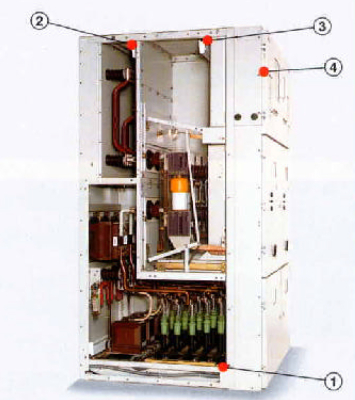
Fitting of the sensors in a partitioned switch unit. Partitioned switch unit type WKC, arrangement of sensors in circuit breaker, outgoing cable and busbar compartments. 1. Sensor in outgoing cable compartment 2. Sensor in busbar compartment 3. Sensor in circuitbreaker compartment 4. Arc detector fitted in relay cabinet
Planning the arc detection System calls for accurate knowledge of its technology and possible effects of arcing.
In the switchgear the sensors of the arc detection system must be so arranged that every arc is detected. Consequently a sensor must be fitted in every compartment.
In large compartments (e.g. busbar compartment without unit unit partitioning) a sensor must be provided about every three metres.
Checking the serviceability
01 the arc detection system LBW takes place using a flashgun test circuit without breaker in question). Testing takes place either direct or by means of fibre-optic waveguides which may be laid between sensors and enclosure.
When the arc detection system is used in SF6-insulated switchgear, the light-sensitive sensors must be mounted outside the switchgear in front of small inspection windows. This arrangement also offers the merit of easy testing of the serviceability of the arc detection System at all times.
By means of a separate DC transformer direct disconnection of the arc disconnection system is ensured.
Sensor of a protected area may be connected to a common amplifier or a common relay combination.
Technical data ot the system components
Mechanical data: as a PCB the arc detector is housed in a standard LRB case with screw terminals at both ends and all signal inputs on one end.
Electrical data
Supply voltage:
+UB = 24 V (+10% / -20%)
Closed-circuit current:
7mA (+10% / -20%)
Max. current capacity:
4OmA (+10% / -20%)
General technical data
Service temperature:
Amplifier: -20° to 70 °C
Sensor: -25° to 85° C
Test voltage: 2000 V
Protective categories:
Amplifiers: IP 53
Sensors : IP 65
The other system components needed for dis - connection of the defective area (transformers, over- current relays and circuit breakers) must be rated in compliance with the switchgear requirements.
Retrofitting existing switchgear with the arc detection systems LBW
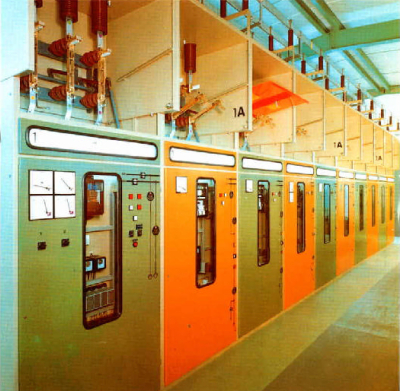
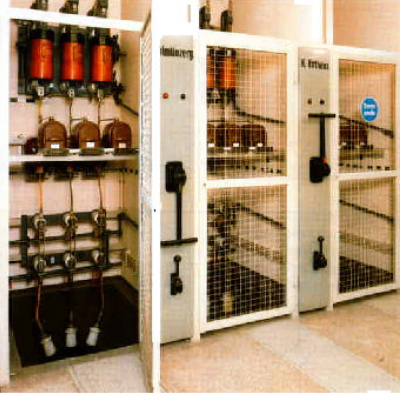
Metal-enclosed switchgear which comply with the requirements for protection against contact but for which staff safety in the event of arcing has not been proved, may be retrofitted with the system LBW.
In this manner arcing safety may be assured and the effects of arcing reduced. At various accessible sides open switchgear may be provided with guards instead of with protective covers to provide a defined protection against contact.
The guards may be rails, chains or trellised walls or gates.
In general adherence to the requirements for arc resistant switchgear as regards protection against contact and stability of the switchgear building, cannot be expected for such installations. By retrofitting the arc detection system LBW and additional measures if necessary, the effects of internal arcing may be limited.
Schematic
A busbar section is disconnected as shown in drawings 1 and 2.
If the disconnection of a complete busbar section is allowed on the occurrence of an arc, the design may comply with drawing 1, whereby up to twenty sensors may be connected to an arc detection system.
The protection principle of the arc detection system incorporates two important criteria:
- dynamic rise of light intensity (corresponding to an arc)
- overcurrent in the feed-in unit.
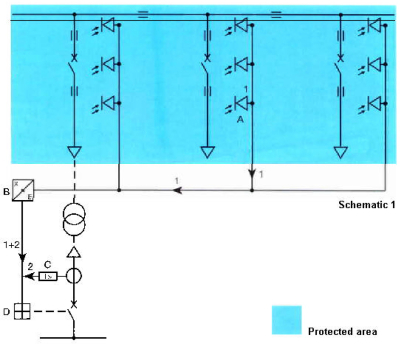
Drawing 1
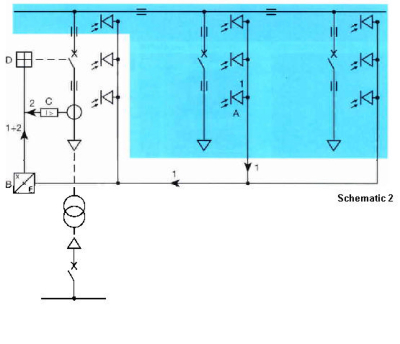
Drawing 2
Action (drawings 1 and 2)
1. On arc ignition the change of radiation on the sensor (A) is evaluated by the arc detection unit (B) through the connection (1).
If the exchange exceeds the preset value the contact position of a relay in the arc detection system (B) is changed.
2. The overcurrent relay © in the feed-in unit (2) applies the release voltage to the feed-in switch (D) through the change relay contact position and this disconnects the protect area.
Excerpts
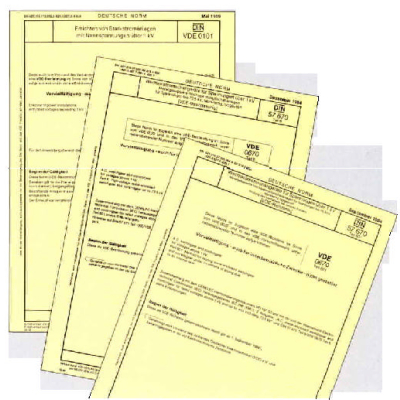
Excerpt from DIN VDE0101 Installation of high-voltage systems for rated voltages Above 1kV
“.4.4 Systems for protection on control must be so designed that staff is protected in high degree. This condition is satisfied if one of the following or equivalent measures is provided:
a) Switch instead of disconnector. Switch-disconnectors must be able to disconnect the maximum normal current arising in the installation and be suitable for making after short-circuits
b) Protection for errors of control for disconnectors and earthing switches,
e. g. interlocks, earthing switches resistant to making, non-interchangeable key locks.
c) Equipment control from safe distance.
d) Fitting of suitable protective devices, e.g. arc guide plates, arc windows, fulllength doors, partition walls.”
Excerpt from DIN VDE 0670 part 6
Metal-enclosed HV switchgear for voltages up to 72.5kV, factory assembled, type-tested:
“Table AA2.Examples of measures to limit the effects of internal defects
- very short response time, e.g. through light, pressure or temperature-sensitive detectors or through busbar differential protection
- use of suitable fuses in combination with switch-gear to limit the let-through current and defect duration.
- low dwell probability e.g. by remote control
- pressure relief flaps.”
Excerpt fom DIN VDE 0670 part 601
Testing behaviour after internal defects
“Appraisal of test.
The following criteria take into account the arc effects men-tioned in section 1. The test customer must decide on the basis of which criteria the test results shall be appraised.
In detal:
Criterion No. 1
Whether or not properly secured doors, covers, etc. do not open
Criterion No. 2
Whether not parts fly off the (metal-enclosed switchgear) with could jeopardise staff. They include large parts with sharp edges like inspection windows, pressure relief flaps cover plates etc. made of metal or plastic.
Criterion 3
Whether or not holes are made through the effect of arcing in the freely accessible upper parts of the enclos ure through burning or other effects.
Criterion 4
Whether or not indicators applied perpendicularly (cf. section 5.3) are set on fire. Indicators ignited by burning varnish or burning labels are precluded from this appraisal.
Critorion 5
Whether or not indicators applied horizontally are set on fire (cf. section 5.3.). Should they start to burn during the test, the criterion shall nevertheless be considered satisfied insofar as can be proved that they were ignited by glowing particles and not by hot gases. Proof shall be furnished by means of a high-speed camera.
Criterion 6
Whether or not all earth con-nections are effekctive.”